5 Steps Warehouse Management
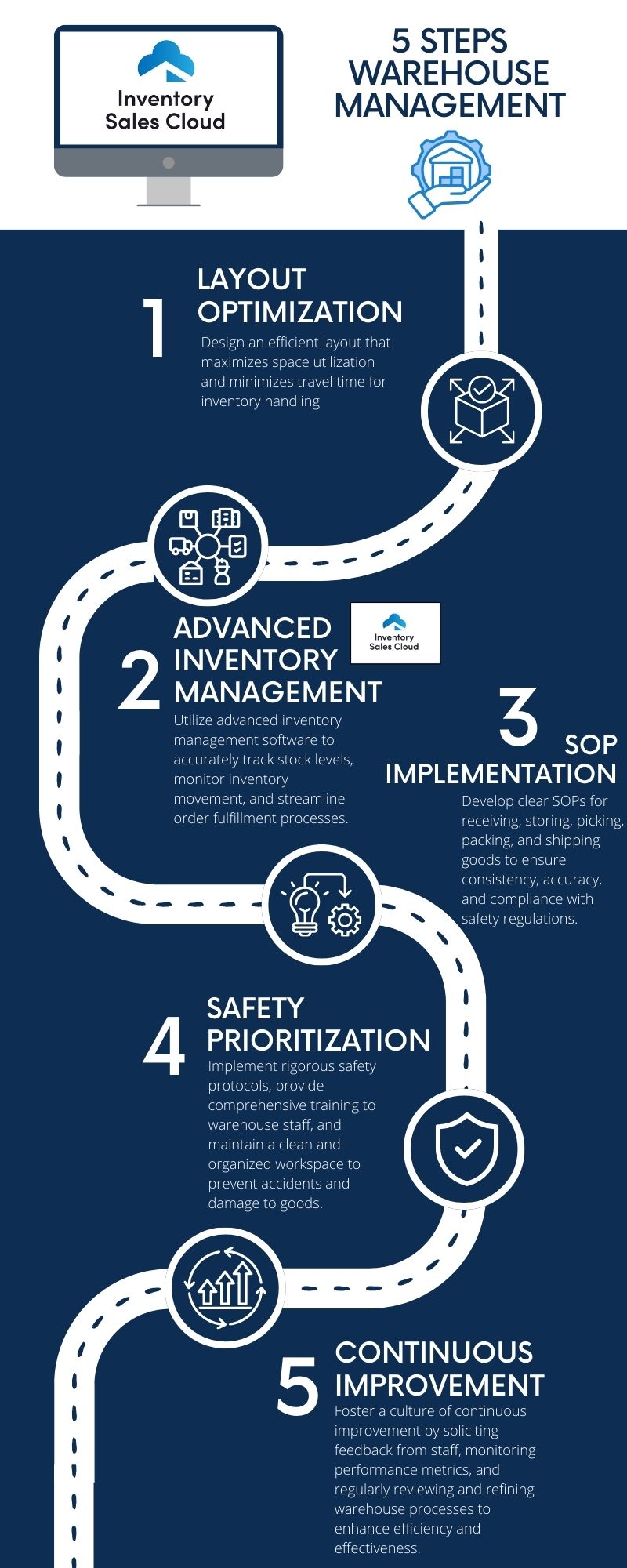
- Layout Optimization
A well-designed warehouse layout is the foundation of efficient operations. Focus on:- Zoning: Separate areas for receiving, storage, picking, packing, and shipping to minimize cross-traffic and confusion.
- Accessibility: Place high-demand or fast-moving items closer to packing and shipping areas to reduce travel time.
- Vertical Space Utilization: Use vertical storage solutions like racks and shelves to maximize available space without expanding the footprint.
- Clear Signage: Label aisles, shelves, and zones clearly to improve navigation and reduce picking errors.
Regularly review and adjust the layout as inventory and operational needs evolve.
- Advanced Inventory Management
Leverage technology to stay on top of inventory control:- Real-Time Tracking: Use barcodes, RFID, or QR codes integrated with inventory management software to monitor stock movement in real-time.
- Demand Forecasting: Analyze historical data to predict demand and prevent overstocking or stockouts.
- Automated Reordering: Set up automated reorder points for critical items to maintain optimal stock levels.
- Integration: Connect inventory systems with sales platforms, accounting software, and supply chain tools for seamless operations.
This reduces errors, speeds up order fulfillment, and ensures accurate stock visibility.
- SOP Implementation
Standard Operating Procedures (SOPs) create consistency and reliability in warehouse operations:- Receiving Goods: Include steps for verifying shipment accuracy, inspecting goods, and updating inventory records.
- Storage: Define guidelines for organizing items based on categories, demand frequency, or size.
- Order Picking: Adopt efficient picking methods like batch picking, wave picking, or zone picking, depending on order volume.
- Packing and Shipping: Ensure proper packaging to protect goods during transit and use automated shipping labels for accuracy.
- Regular Training: Train employees on SOPs to maintain high standards and compliance with safety and quality regulations.
- Safety Prioritization
Safety is crucial for protecting employees, inventory, and equipment:- Training: Conduct regular safety training sessions to educate staff on equipment handling, emergency procedures, and hazard identification.
- Equipment Maintenance: Regularly inspect and maintain forklifts, conveyor belts, and other machinery to prevent malfunctions.
- Ergonomics: Provide tools like adjustable workstations and lifting aids to reduce strain on employees.
- Cleanliness: Keep aisles clear, remove debris, and ensure proper lighting to reduce risks of slips, trips, and falls.
- Compliance: Adhere to local and international safety standards to avoid legal and financial penalties.
- Continuous Improvement
Warehousing is an evolving process that benefits from ongoing refinement:- Performance Metrics: Monitor KPIs such as order accuracy, cycle time, inventory turnover, and picking speed to identify areas for improvement.
- Feedback Loops: Regularly solicit feedback from warehouse staff to uncover inefficiencies or potential bottlenecks.
- Technology Upgrades: Stay updated with advancements like warehouse robotics, AI-driven analytics, and IoT sensors to enhance productivity.
- Regular Audits: Conduct periodic reviews of processes, equipment, and layout to ensure alignment with business goals and industry standards.
- Employee Engagement: Foster a culture where employees feel empowered to suggest changes and participate in process improvements.
By implementing these steps, warehouses can achieve higher efficiency, reduce operational costs, and improve customer satisfaction, all while ensuring a safe and productive environment.